Comprehensive Guide: What is Porosity in Welding and How to stop It
Comprehensive Guide: What is Porosity in Welding and How to stop It
Blog Article
Porosity in Welding: Identifying Common Issues and Implementing Ideal Practices for Prevention
Porosity in welding is a pervasive issue that commonly goes unnoticed up until it triggers considerable problems with the honesty of welds. In this discussion, we will explore the essential factors contributing to porosity development, examine its destructive effects on weld efficiency, and review the finest practices that can be embraced to reduce porosity event in welding processes.
Common Root Causes Of Porosity
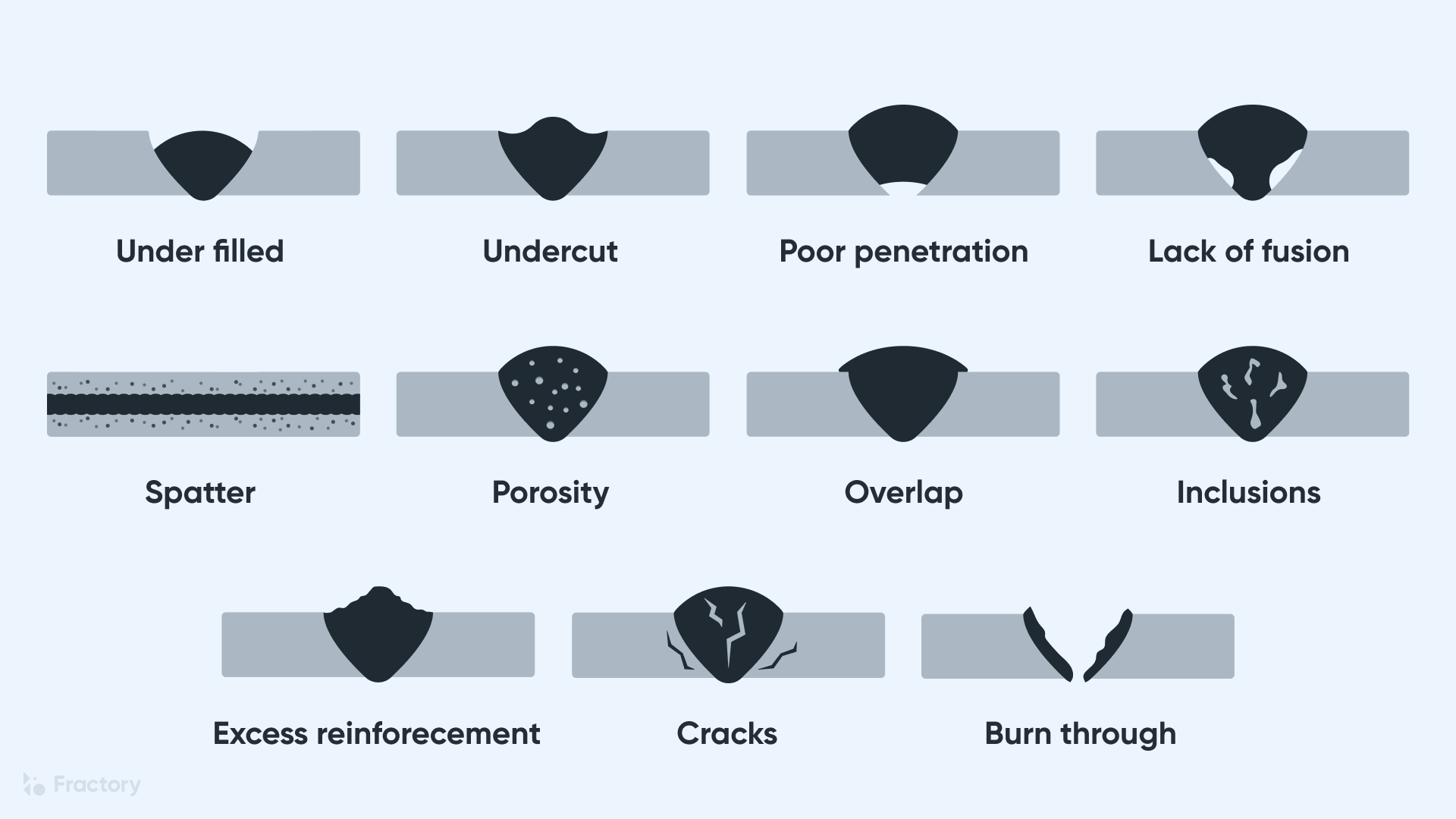
Making use of dirty or wet filler products can introduce impurities into the weld, contributing to porosity issues. To mitigate these usual causes of porosity, thorough cleansing of base metals, correct shielding gas selection, and adherence to ideal welding criteria are essential methods in accomplishing top notch, porosity-free welds.
Impact of Porosity on Weld Top Quality

The existence of porosity in welding can considerably compromise the architectural stability and mechanical homes of welded joints. Porosity develops spaces within the weld metal, compromising its general toughness and load-bearing ability.
Welds with high porosity degrees tend to show lower effect toughness and decreased capacity to warp plastically prior to fracturing. Porosity can restrain the weld's capacity to successfully send forces, leading to early weld failing and potential security hazards in important structures.
Best Practices for Porosity Avoidance
To enhance the architectural integrity and high quality of bonded joints, what specific actions can be applied to lessen the incident of porosity during the welding process? Making use of the right welding method for the details product being welded, such as readjusting the welding angle and gun placement, can better stop porosity. Routine evaluation of welds and immediate removal of any type of issues identified throughout the welding process are important practices to prevent porosity and create high-grade welds.
Significance of Proper Welding Strategies
Carrying out proper welding strategies is critical in ensuring the architectural stability and quality of bonded joints, building on the structure of reliable porosity avoidance procedures. Welding methods directly affect the overall strength and durability of the bonded framework. One essential aspect of appropriate welding methods is preserving the appropriate warmth input. Too much warm can result in increased porosity as a result of the entrapment of gases in the weld pool. Conversely, not enough warm may lead to insufficient fusion, developing prospective weak points in the joint. In addition, using the ideal welding criteria, such as voltage, existing, and take a trip speed, is vital for achieving sound welds with marginal porosity.
Additionally, the option of welding procedure, whether Find Out More it be MIG, TIG, or stick welding, must line up with the particular requirements of the task to make sure optimal outcomes. Appropriate cleansing and prep work of the base metal, along with choosing the best filler product, are likewise important components of skillful welding methods. By adhering to these ideal practices, welders can reduce the risk of porosity development and create top quality, structurally audio welds.
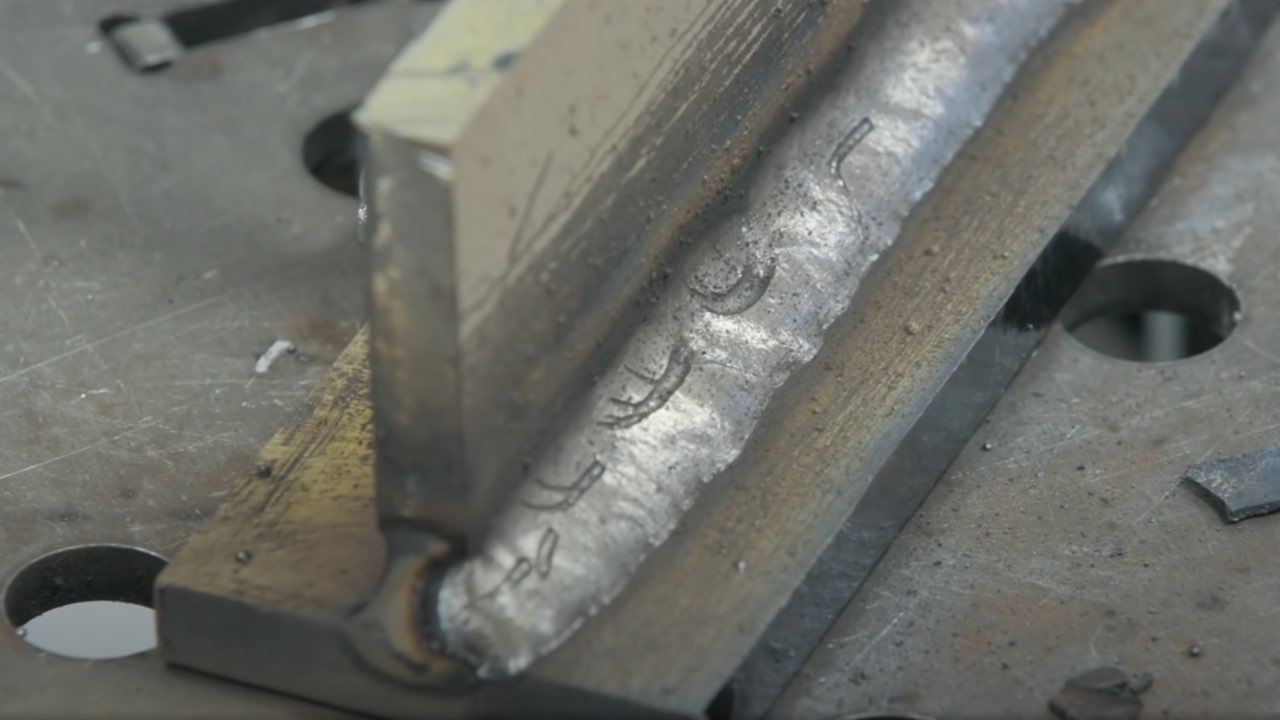
Checking and High Quality Control Measures
Testing treatments are crucial to identify and protect against porosity in welding, making sure the stamina and sturdiness of the last item. Non-destructive testing methods such as ultrasonic screening, radiographic screening, and visual evaluation are commonly used to click here now determine prospective defects like porosity.
Conducting pre-weld and post-weld assessments is also essential in preserving quality control requirements. Pre-weld examinations include verifying the products, equipment setups, and cleanliness of the workspace to prevent contamination. Post-weld evaluations, on the other hand, analyze the final weld for any type of flaws, consisting of this page porosity, and confirm that it satisfies defined standards. Implementing a detailed quality control strategy that includes comprehensive testing treatments and examinations is extremely important to lowering porosity problems and making certain the overall top quality of welded joints.
Final Thought
Finally, porosity in welding can be an usual concern that influences the top quality of welds. By identifying the common reasons for porosity and executing best practices for prevention, such as appropriate welding strategies and screening measures, welders can make sure excellent quality and reputable welds. It is necessary to prioritize prevention techniques to lessen the incident of porosity and keep the honesty of bonded frameworks.
Report this page